Live 3D printing of metallic alloys probed with synchrotron light
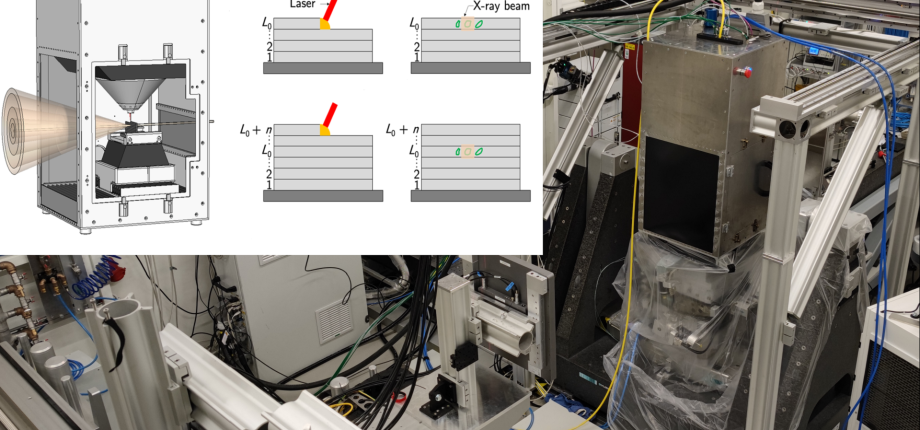
Metals, even strong metallic alloys such as stainless steels, can be bent, pulled or twisted to some extent without breaking. This deformation capacity is due to dislocations, that are very small defects at the microscopic level in the otherwise very regular atomic lattice. Dislocations can for instance slip on lattice planes in tiny movements that allow the material to permanently deform under applied load. Therefore, as far as additive manufacturing is concerned, it is promising to control the amount and the arrangements of these defects. “But first, we have to understand when dislocations form and how do they evolve during the 3D printing of metallic alloys” says Manas Upadhyay. This researcher from the Solid Mechanics Laboratory (LMS*), and an Assistant Professor at École Polytechnique (Institut Polytechnique de Paris), has led a study published in the journal, Additive Manufacturing, which shows that dislocations formed during 3D printing undergo significant evolution in the subsequent phases of the process.
Two competing hypotheses
Three phenomena occur during this kind of fabrication. The metallic powder feedstock is melted and deposited, then it rapidly solidifies in a few seconds. Finally, the material undergoes cooling and heating cycles in the solid-state as more layers are deposited on top of each other. Scientists knew that dislocations form during solidification. But do dislocations evolve during this solid-state thermal cycling or not? These two hypotheses concerning their evolution were only based on studies of samples already printed that couldn’t differentiate the role of the solidification and of the solid-state thermal cycling phases.
In this study, the experiments were conducted using a newly designed miniature laser metal deposition machine, which has been transported to the beamline P21.2 at PETRA III, the synchrotron light source at DESY in Hamburg. This beamline is well-suited for X-ray diffraction, i.e. to observe the internal structure of the material, live during 3D printing. The X-ray beam is rather small (300 x 300 µm2), and can be focused on one layer of the stainless steel sample being printed through a window made in the 3D printing device. One layer of material is made up of multiple “grains” next to each other. Each grain is an arrangement of atomic lattice planes having the same orientation that are different from neighbouring grains. In the material studied in this work, the grains were a few tens of micrometres in size. When the X-ray beam illuminates those grains of different lattice orientation, it creates a so-called diffraction pattern detected several meters away. This pattern exhibits several spots, containing information about the microscopic structure of the metallic alloy. “Looking at one of these spots allows us to identify a single grain and follow its evolution, which is important because dislocations are present within each grain” explains Manas Upadhyay. This technique, called high-resolution reciprocal space mapping, has been in particular pioneered by Wolfgang Pantleon (Technical University of Denmark) and Ulrich Lienert (DESY), who are co-authors of this study.
Promising perspectives
After printing a few layers of the material, the researchers selected five spots corresponding to five different grains in the top layer whose structure was observed using the X-ray beam. Then, they printed a few more layers and focus the beam on to the exact same grains to see how they evolved. By repeating this procedure, they could conclude without any doubt that the dislocation structure formed during solidification was significantly changing during solid-state thermal cycling. This new result is decisive because it settles the debate in favour of one of two competing hypotheses and it opens the way for new experiments to understand more precisely the fundamental mechanisms governing the formation of dislocations and eventually tailoring their formation to design materials with desired mechanical properties.
This research is funded by the European Research Council through the project GAMMA led by Manas Upadhyay. The EuroTech Visting Researcher Program also supported this work.