L'impression 3D des métaux sondée en direct par rayonnement synchrotron
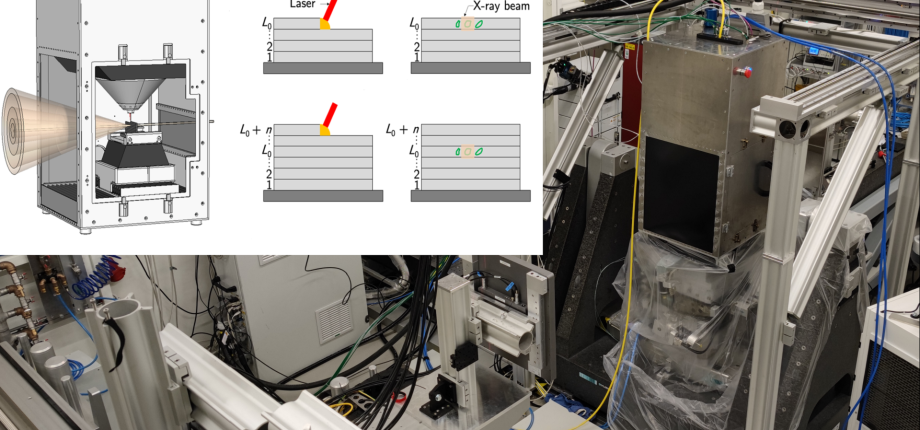
Les métaux, même les alliages métalliques résistants comme l'acier inoxydable, peuvent être pliés, tirés ou tordus dans une certaine mesure sans se briser. Cette capacité de déformation est due aux dislocations, qui sont de très petits défauts au niveau microscopique dans le réseau atomique par ailleurs très régulier. Les dislocations peuvent par exemple glisser sur les plans du réseau en effectuant de légers mouvements qui permettent au matériau de se déformer de manière permanente sous l'effet d'une charge appliquée. Par conséquent, dans le cadre de la fabrication additive, il semble prometteur de contrôler la quantité et l'emplacement de ces défauts. "Mais d'abord, nous devons comprendre quand les dislocations se forment et comment elles évoluent pendant l'impression 3D d'alliages métalliques", explique Manas Upadhyay. Ce chercheur du Laboratoire de mécanique des solides (LMS*) et professeur assistant à l'École polytechnique (Institut polytechnique de Paris), a dirigé une étude publiée dans la revue Additive Manufacturing, qui montre que les dislocations formées lors de l'impression 3D subissent une évolution significative dans les phases ultérieures du processus.
Deux hypothèses concurrentes
Trois phénomènes se produisent au cours de ce type de fabrication. La poudre métallique est fondue et déposée en couches, puis elle se solidifie rapidement en quelques secondes. Enfin, le matériau subit des cycles de refroidissement et de chauffage à l'état solide au fur et à mesure que d'autres couches sont déposées les unes sur les autres. Les scientifiques savaient que les dislocations se forment pendant la solidification. Mais deux hypothèses restaient possibles : les dislocations évoluent-elles ou non au cours de ce cycle thermique à l'état solide ? Ces deux hypothèses étaient uniquement basées sur des études d'échantillons déjà imprimés qui ne permettaient pas de différencier le rôle de la phase de solidification de celui du cycle thermique à l'état solide.
Dans cette étude, les expériences ont été menées à l'aide d'une machine de dépôt de métal par laser spécialement conçue qui a été transportée sur la ligne de faisceau P21.2 du synchrotron PETRA III, une source de rayons X située au Deutsches Elektronen-Synchrotron facility (DESY) à Hambourg, en Allemagne. Cette ligne de faisceau est bien adaptée à la diffraction des rayons X de haute énergie, donc à l'observation de la structure interne du matériau, en direct lors de l'impression 3D. Le faisceau de rayons X est relativement petit (300 x 300 µm2) et peut être focalisé sur une couche de l'échantillon d'acier inoxydable en cours d'impression à travers une fenêtre pratiquée dans la machine. Une couche de matériau est constituée de plusieurs "grains" juxtaposés. Chaque grain est un arrangement de plans de réseau atomique ayant la même orientation, mais différente de celle des grains voisins. Dans le matériau étudié dans ce travail, les grains avaient une taille de quelques dizaines de micromètres. Lorsque le faisceau de rayons X illumine ces grains aux orientations différentes, il crée une figure de diffraction détectée à plusieurs mètres de distance. Cette figure présente plusieurs taches qui contiennent des informations sur la structure microscopique de l'alliage métallique. "Regarder l'une de ces taches revient à suivre un seul grain, ce qui est important car des dislocations sont présentes dans chaque grain", explique Manas Upadhyay. Cette technique, appelée cartographie de l'espace réciproque à haute résolution (high-resolution reciprocal space mapping), a notamment été mise au point par Wolfgang Pantleon (Université technique du Danemark) et Ulrich Lienert (DESY), qui sont coauteurs de cette étude.
Des perspectives prometteuses
Après avoir imprimé quelques couches du matériau, les chercheurs ont sélectionné cinq points correspondant à cinq grains différents dans la couche supérieure, dont la structure a été observée grâce au faisceau de rayons X. Ils ont ensuite imprimé quelques couches supplémentaires et focalisé le faisceau sur les mêmes grains pour voir comment ils évoluaient. En répétant cette procédure, ils ont pu conclure sans aucun doute que la structure de dislocation formée lors de la solidification changeait de manière significative pendant le cycle thermique à l'état solide. Ce nouveau résultat est décisif car il tranche le débat en faveur de l'une des deux hypothèses concurrentes et ouvre la voie à de nouvelles expériences pour comprendre plus précisément les mécanismes fondamentaux qui régissent la formation des dislocations et éventuellement adapter leur formation pour concevoir des matériaux aux propriétés mécaniques souhaitées.
Cette recherche est financée par le Conseil européen de la recherche dans le cadre du projet GAMMA mené par Manas Upadhyay. Le programme EuroTech Visting Researcher a également soutenu ce travail.